Doosan Horizontal and Milling Machine DBC130L
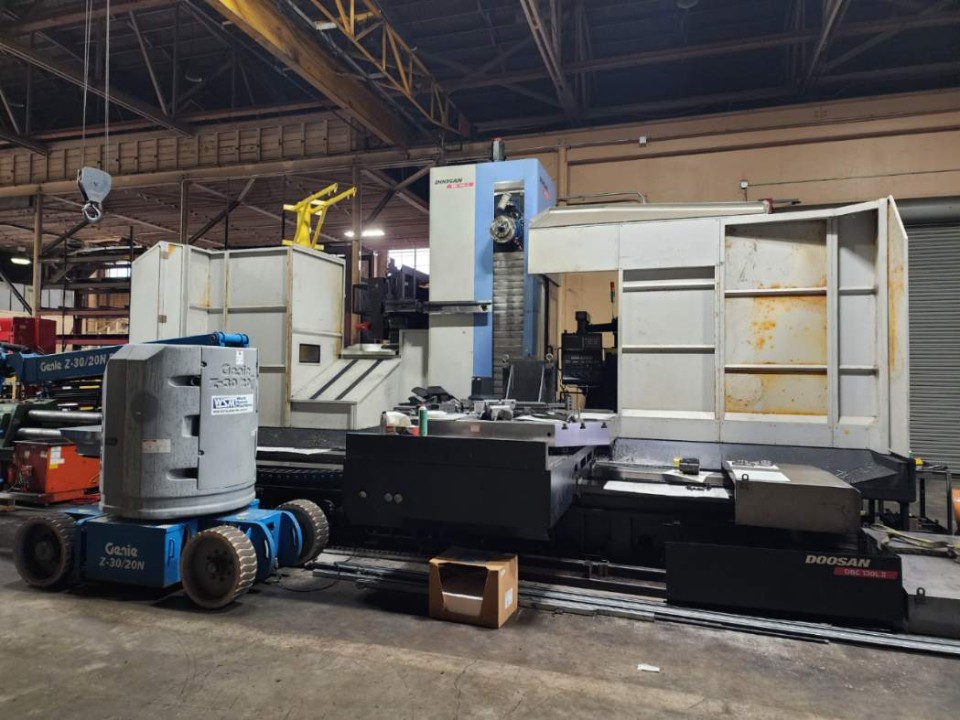
Called in to rebuild the X-Axis ball screw on a Doosan Horizontal Milling Machine DBC130L. This machine was from 2014. This machine and job were common ones received at Ballscrew Guys. The company bought a machine at a good price from an auction. They discovered the axes and ball screws were loose. They realized the reason the machine was discounted was that it could not hold tolerance. The new owners started calling around for new ball screws, then learned that they cost many times more than what they paid for the machine. That was a good time to call us because we specialize in fixing the ball screws at a fraction of the price of buying new.
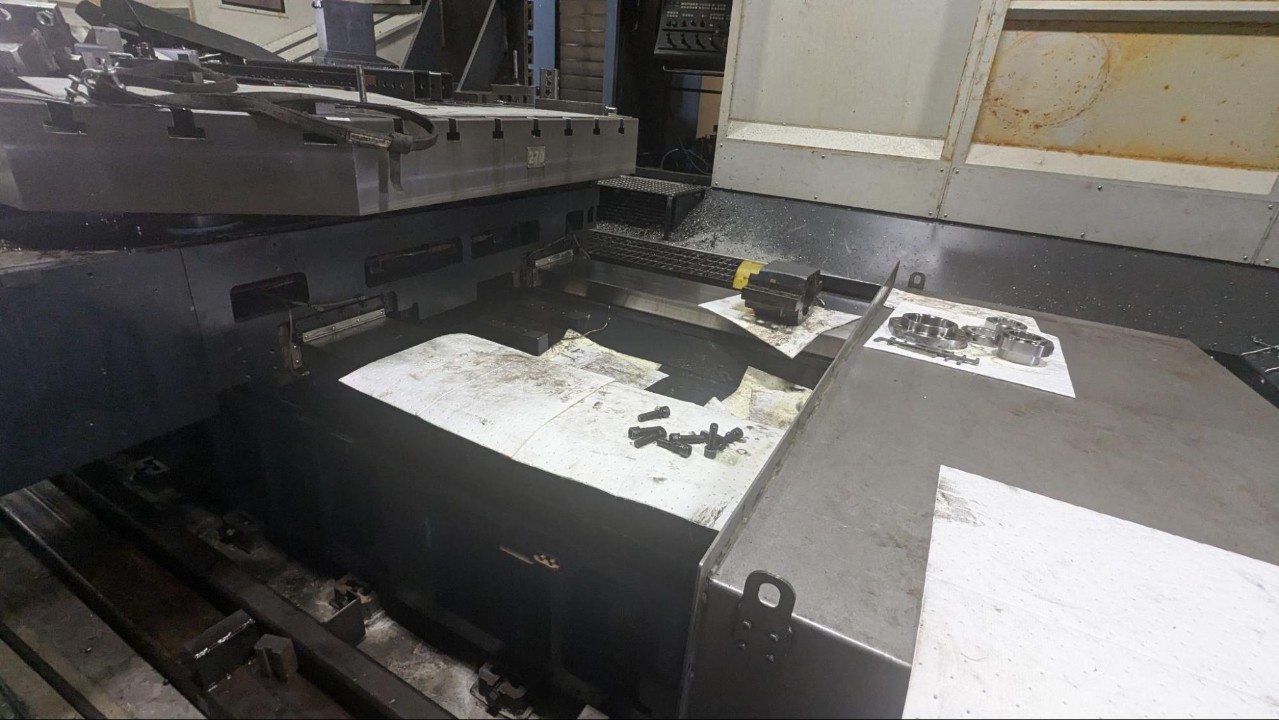
The X-Axis ball screw was pulled out from underneath the table of a Doosan Horizontal and Milling Machine DBC130L. The bolts and end bearing assemblies were laid out. They were then cleaned and inspected. Ballscrew Guys recommended replacing all angular contact end bearing assemblies every time the ball screws were serviced. Verified that ball screw tension was set properly, along with assurance that the assemblies themselves had adequate and proper lubrication.
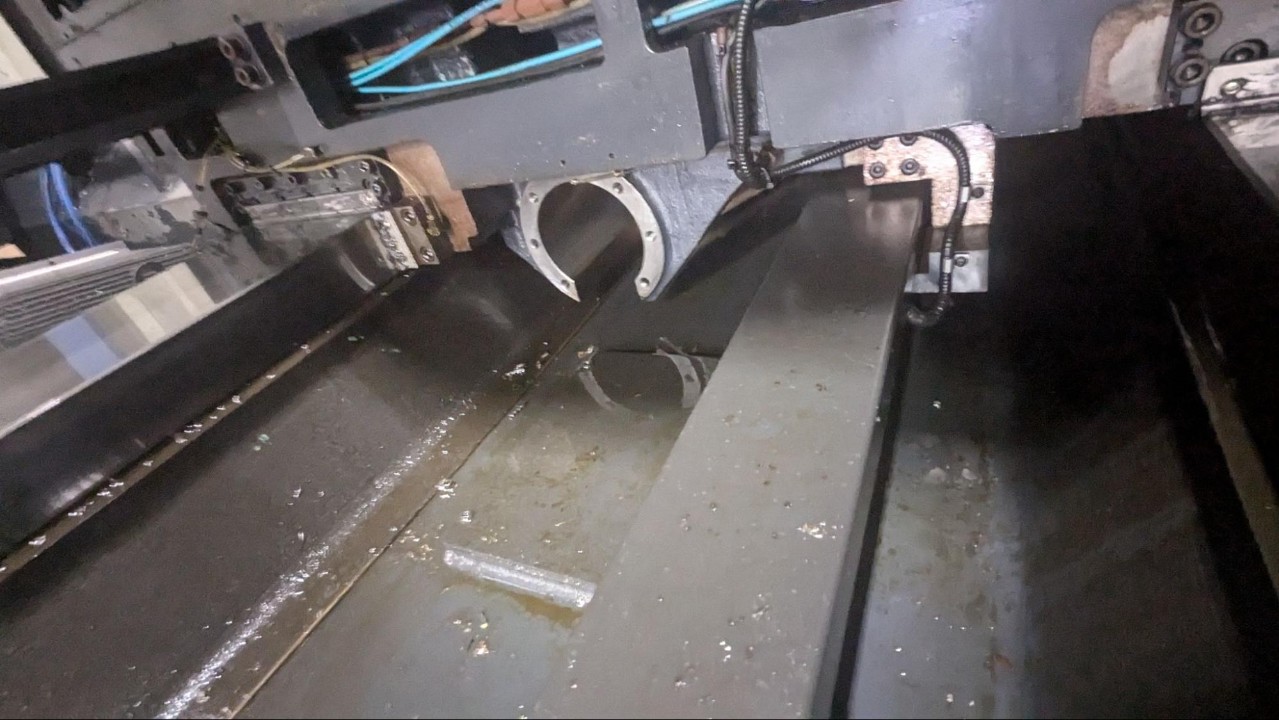
Empty table yoke where the X-Axis ball screw connects. Table slideways are shown. While there is still some savings and debris from the milling and boring processes, this is very clean. When the X-Axis ball screw was being repaired, the slideways were inspected for adequate oil flow and lubrication. The surfaces were cleaned and checked for any damage. The single largest reason why mechanical assemblies wear out on the Doosan DBC130L Horizontal and Milling Machine is because of some sort of lubrication interruption. Whether it was a severed lubrication line, underperforming pump, or preventative maintenance oversight, it must be corrected, or the ball screw will simply wear out prematurely…again.
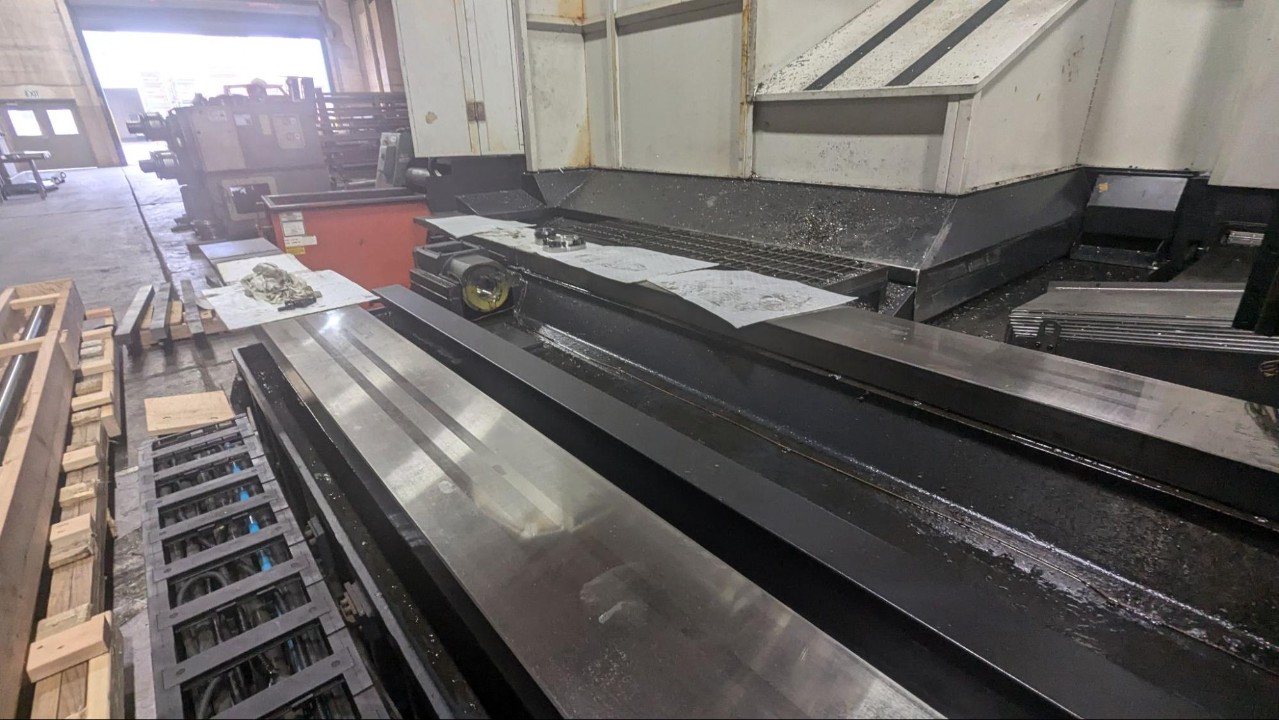
Shown here are the table slideways on a Doosan DBC130L horizontal and milling machine. The X-Axis ball screw has been removed. The motor side end bearing mount has been disassembled. Angular contact bearings have been removed, cleaned, and inspected. New end bearings are always recommended when used ball screws are pulled for service.
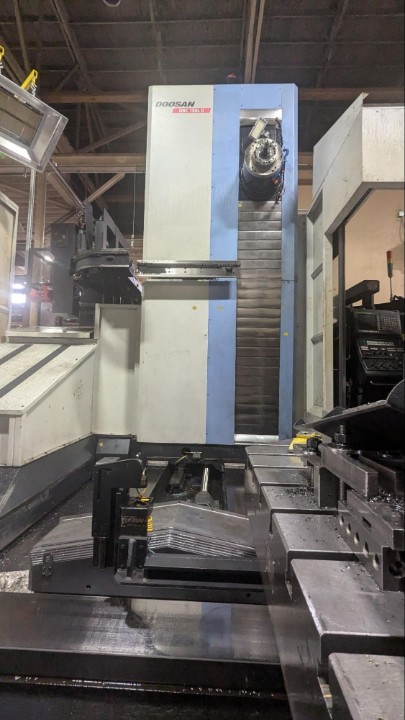
Here is the Y-Axis cutting head tower on a Doosan DBC130L Horizontal Milling Machine. Ballscrew Guys were able to refurbish the Y- and Z-Axis on this machine as well. In most scenarios, however, it was found that the X-Axis, being the ball screw assembly, required service most often. Still, if the machine experienced extended lubrication failure during a production run, these axes desperately needed inspection as well. Ball screws operating without lubrication experienced major wear, often failing during operation.
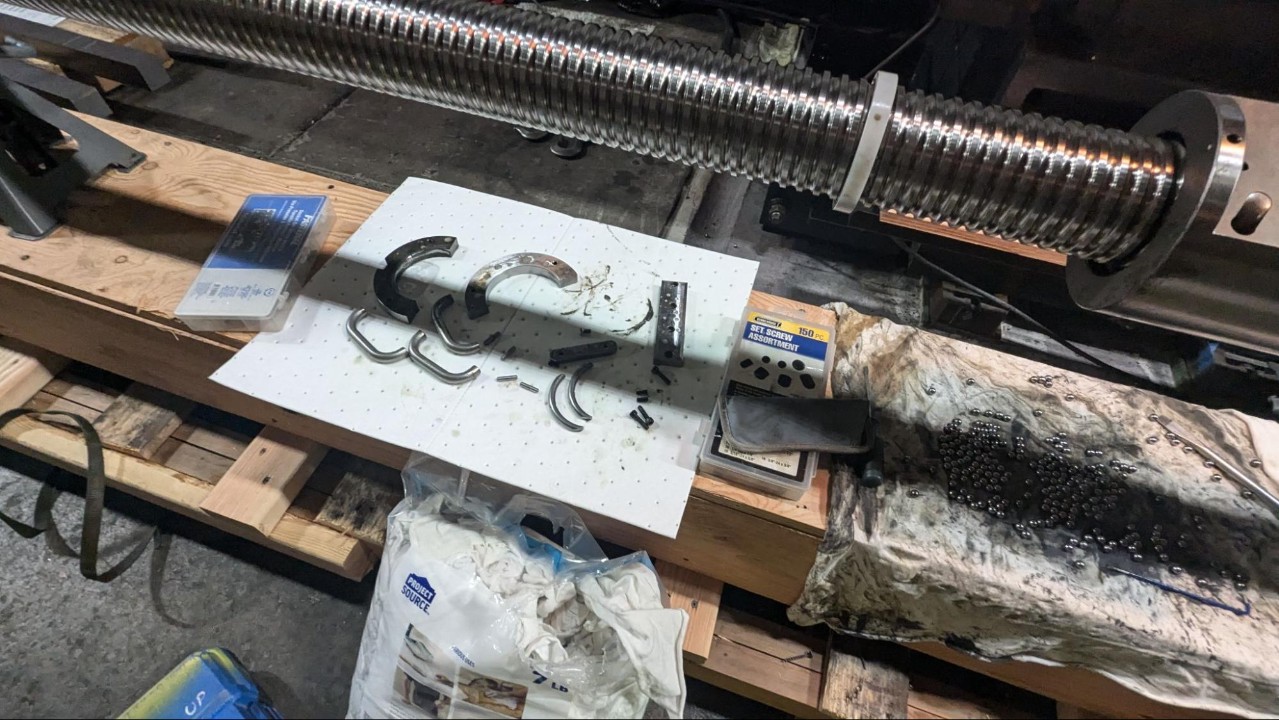
The X-Axis refurbishment process was done next to the machine. In this case, it was a Doosan Horizontal Milling Machine DBC130L. Here, the ball nut was completely disassembled. All parts were cleaned and studied. On this type of milling and boring center, “split-nut” type ball screws were used. Here, there were two separate ball nut halves, spaced by a shim. This allowed each individual ball nut to displace the working load while machining in one particular direction. It was essential that the replacement ball bearings were sized and installed in proportion to the shim size. This is how the working preload for the assembly was established and maintained.
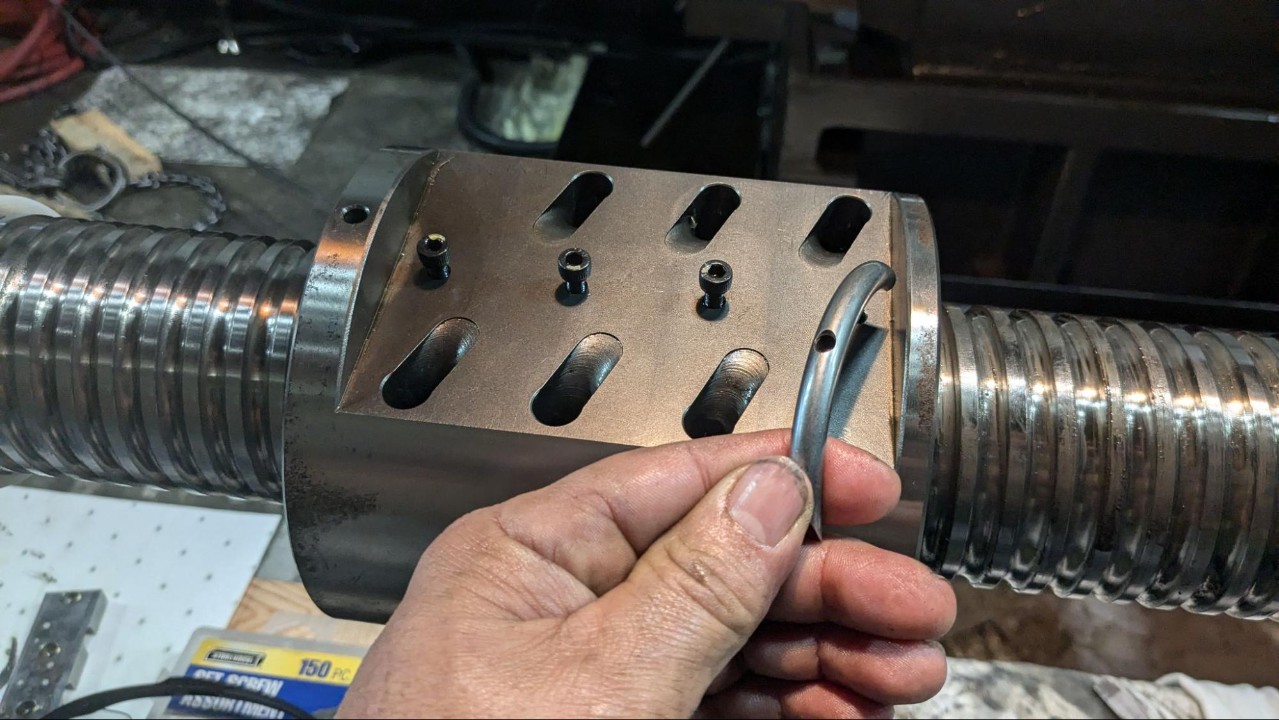
This split nut half was unusual because of the internal ball bearing deflector guides it used. Most ball screw assemblies of this type used an external ball return tube with “ears” that scooped balls up off the ball screw shaft. The “ear” types sometimes got damaged, where the scooping tabs got snapped off. While Ballscrew Guys had certified welders who could rebuild and repair the ball bearing scoops, this design was vastly superior. A solid round bar of steel rode in the groove track, matching the contour of the raceway helix. The solid mass of this scoop would provide decades of durable and reliable service. Doosan chose well in selecting this ball screw.
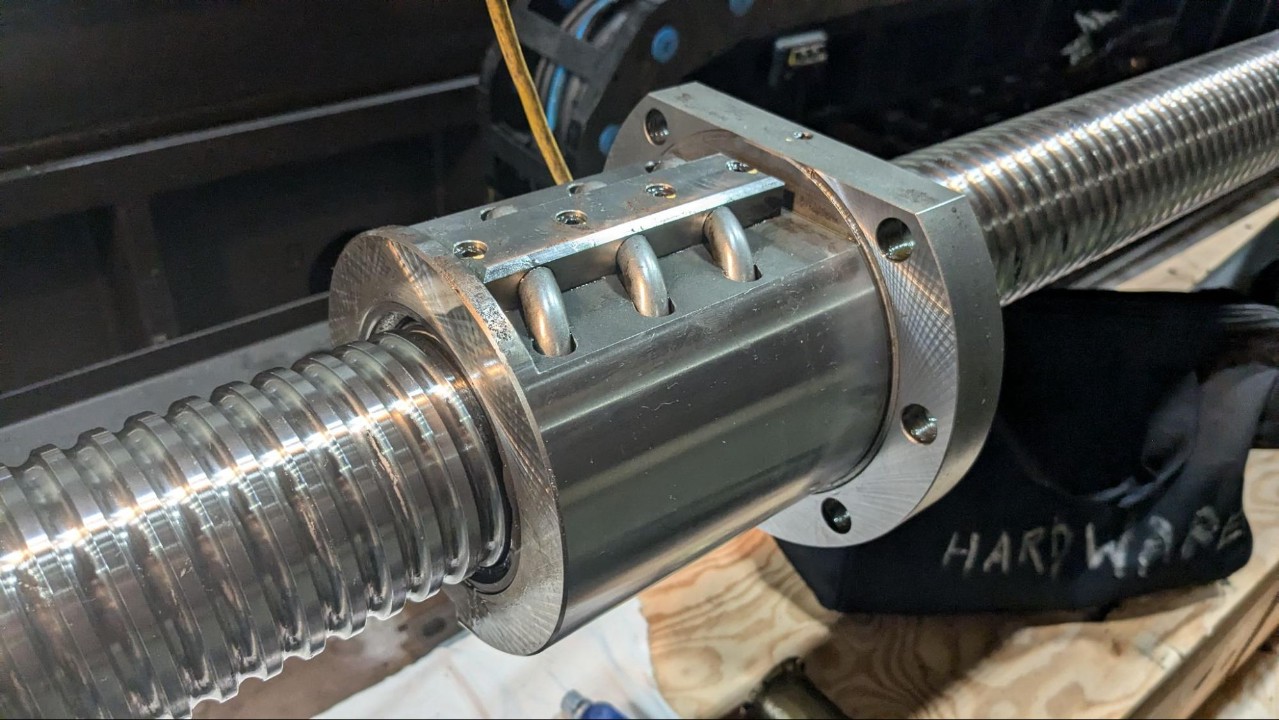
Flange side ball nut half was rebuilt. This is part of the X-Axis ball screw for a Doosan DBC130L. The flange fits into the table yoke on the machine. The ball screws and ball nut components were cleaned and polished. New bearings were installed. Waiting for the follower ball nut half to be completed. Then, both halves of the ball nut were put together on a spacer shim. The connected ball nuts were then tested together to see if they had proper drag torque and preload for the machine process.
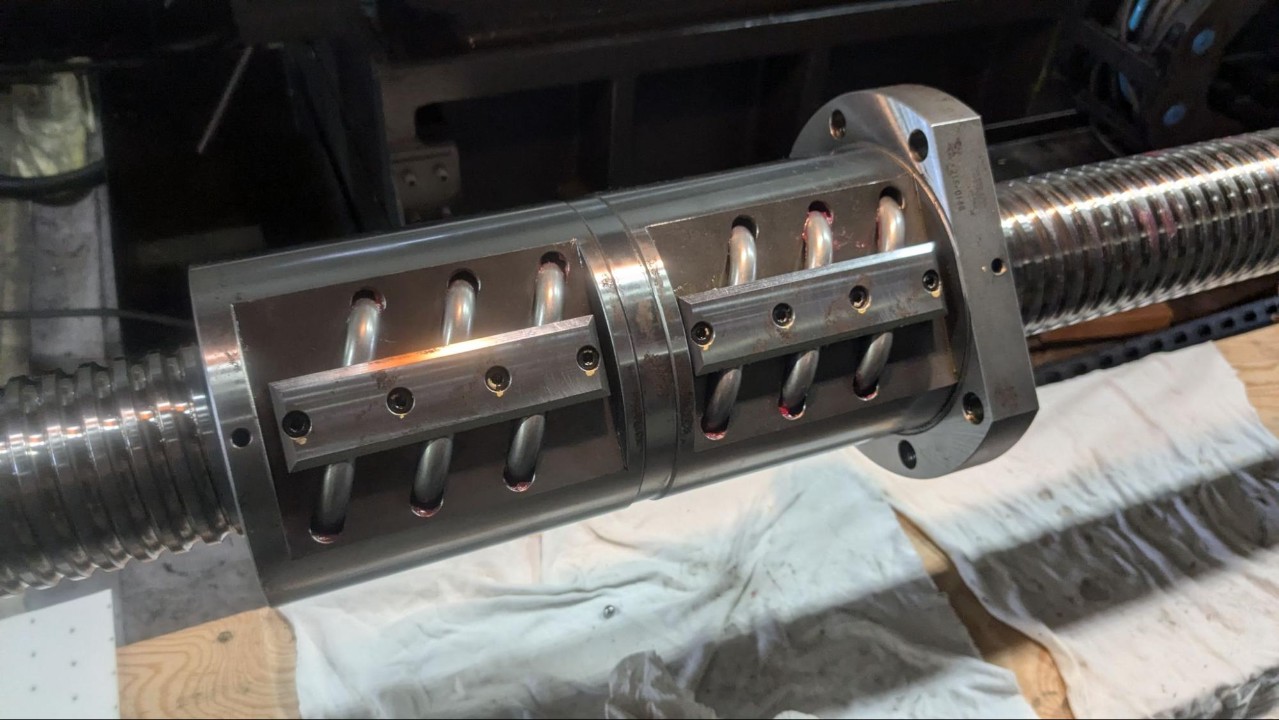
The X-Axis ball screw was installed on a Doosan DBC130L. The ball screw and ball nut components were cleaned and polished. New ball bearings were installed. Here, both halves of the ball nut were put together on either side of a spacer shim. The connected ball nuts were then tested together to see if they had proper drag torque and preload for the machine process. The ball nut was packed with a specialty grease that is soluble with most lubrication oils.
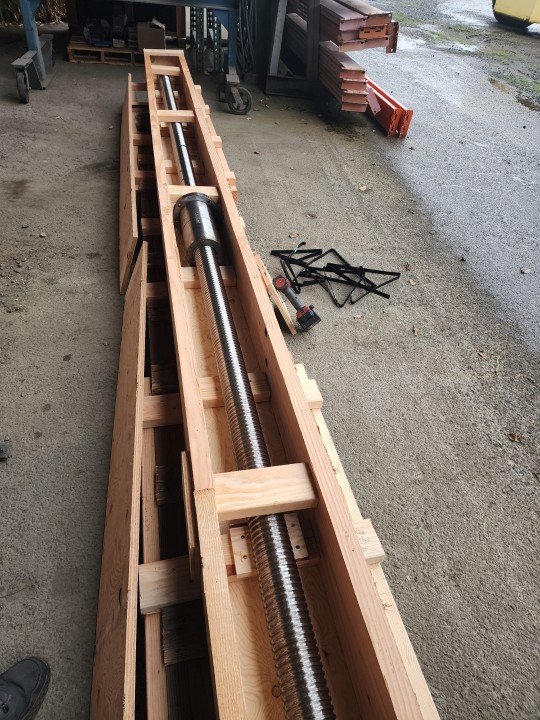
Here, the X-Axis ball screw was packaged in a crate that the owner fabricated. The customer knew the ball screws were worn, so they prepared it for shipment and then started getting quotes for its refurbishment. During this process, they discovered that it was more expensive to ship and insure this ball screw both ways than it was simply to have Ballscrew Guys come and do field service on the ball screw. It saved them months of downtime. The ball screw was able to be refurbished and put back into production for the same price as simply shipping it back and forth to one of our competitors. Less downtime, way lower end cost. Double win for the machine owner.