Hwacheon 35 CNC Turning Lathe (Hieco 35)
Maybe this dinosaur from 1998 looks like your machine. This is a Hwacheon Hi-ECO 35 or Hieco 35 CNC Turning Lathe. We have seen the machine model expressed in many different ways. But still its the same core machine. A CNC Turning Lathe that is often the back bone of many fabrication facilities.
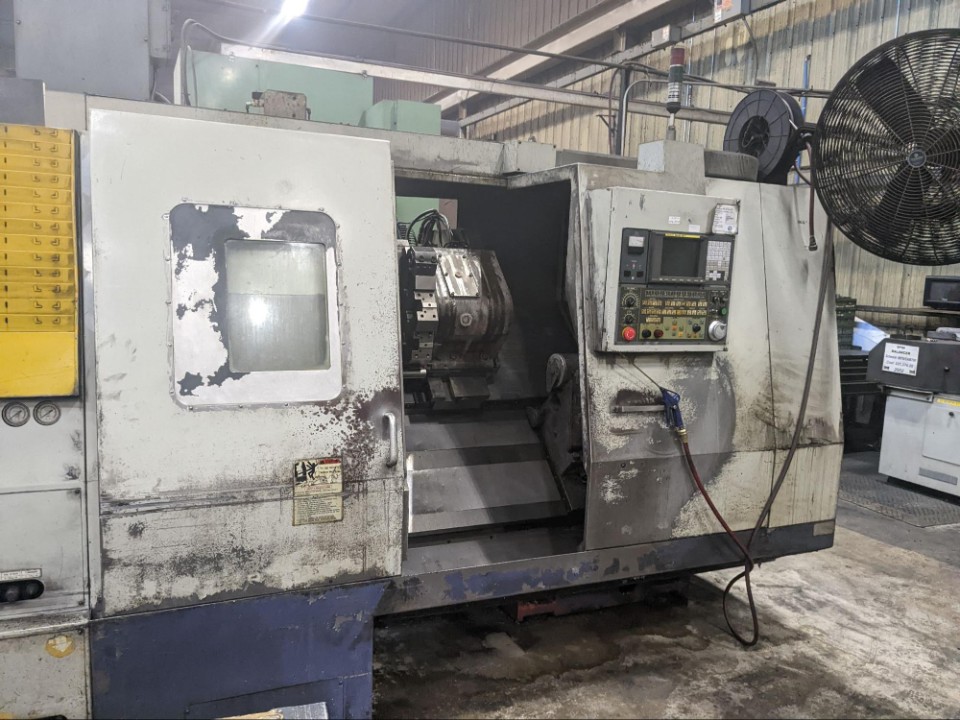
Maybe this dinosaur from 1998 looked like the machine. This is a Hwacheon Hi-ECO 35 or Hieco 35 CNC turning lathe. The machine model was expressed in many different ways, but still, it was the same core machine: a CNC turning lathe that was often the backbone of many fabrication facilities.
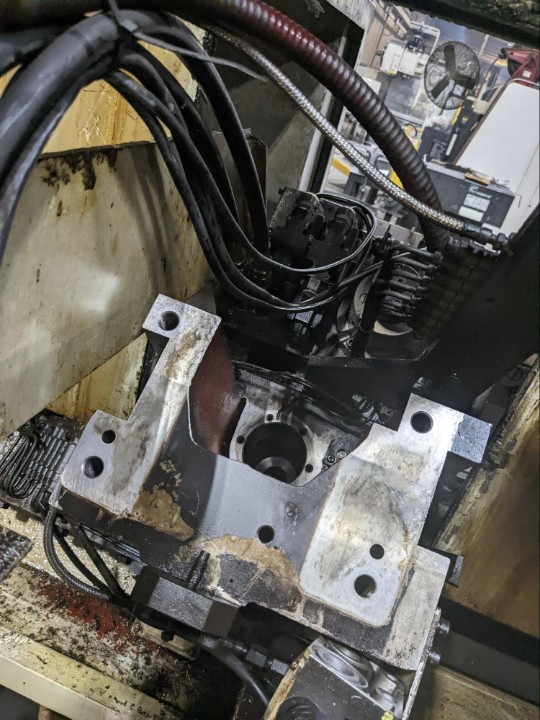
Here, the entire X-Axis was removed from the machine to service this CNC turning lathe. It was a Hwacheon Hi-ECO 35 or Hieco 35 from 1998, using a Japanese NTN ball screw assembly. The X-Axis torque limiter was left in place.
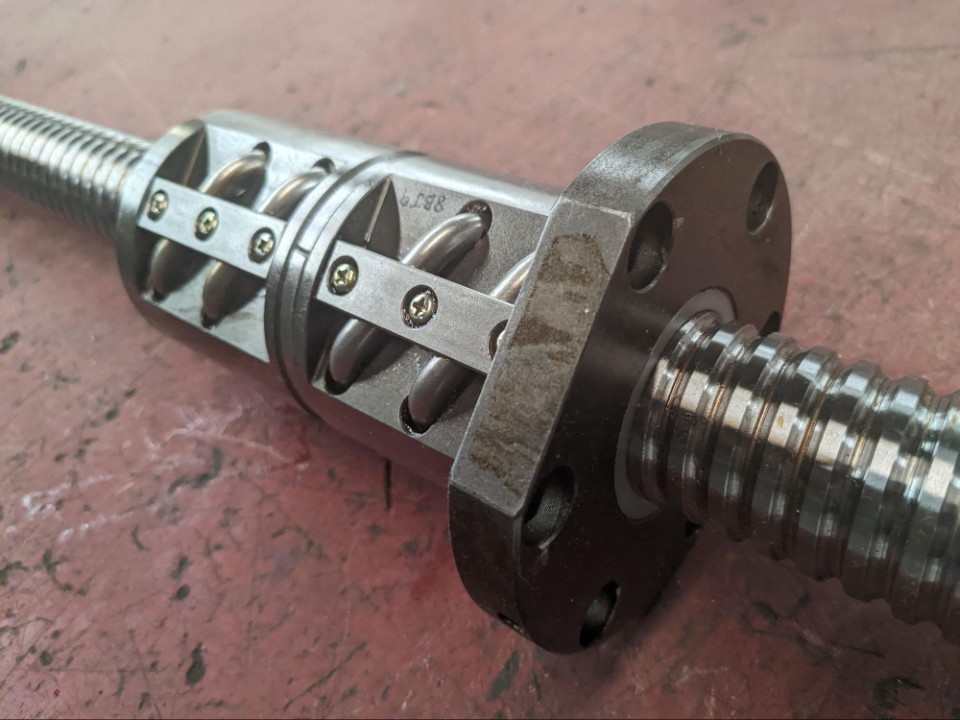
Here is the NTN C3 ball screw being used as the X-Axis in a Hwacheon Hi-ECO 35 or Hieco 35 CNC turning lathe. Notice it is a “split nut” design. This type uses a spacer shim to separate two ball nut halves. The shim spacing must be in proper proportion to the ball bearing size to return preload and adequate drag torque to the ball screw assembly. Some less-than-reputable ball screw repair outfits changed the shim spacing only, leaving worn-out ball bearings. An oversized ball bearing was custom fit to match track wear and balance out the existing shims as they were originally made. This is one of the many differences between the service provided and competitors.
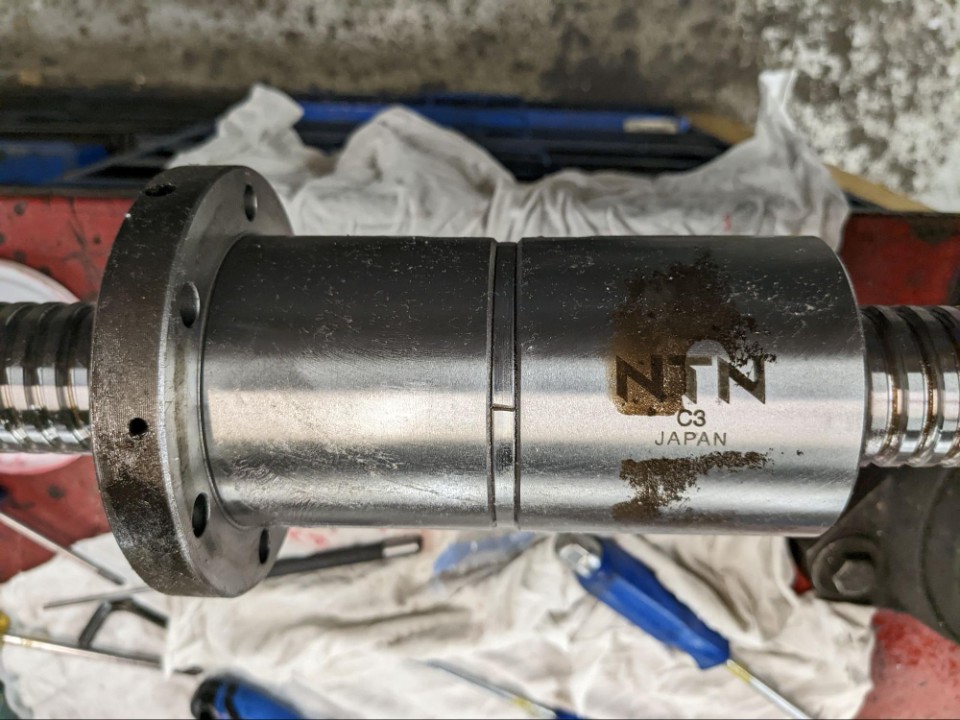
The Japanese NTN C3 ball screw assembly was pulled from the machine. This one was the X-Axis of a 1998 Hwacheon Hi-ECO 35 or Hieco 35 CNC turning lathe. This ball screw may not even be available anymore. Rebuilding the existing screw was lower in cost and downtime compared to waiting for a new ball screw to be fabricated. It was noted that the ball nut is a split nut design. A quick way to see if a machine center like this needs ball screw service is to push those space shims to see if they move. If the ball nut has proper drag torque and preload, those shims should not budge at all. They should be compressed together.
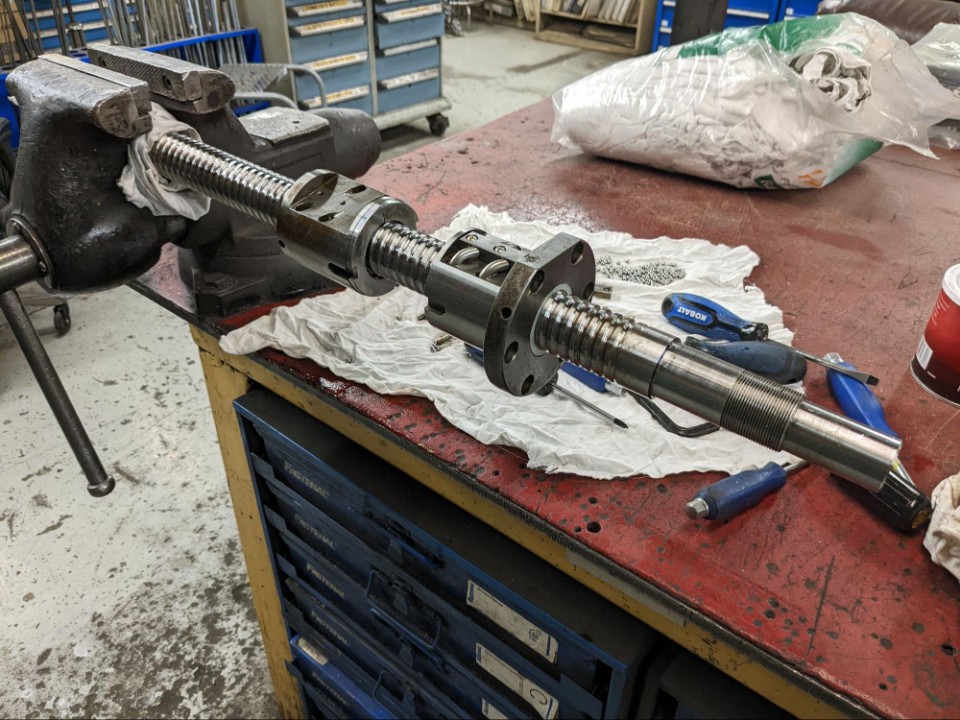
Rebuilt a Japanese NTN C3 ball screw assembly on the bench. If the facility had a talented maintenance staff, Ballscrew Guys were always happy to rebuild ball screws on the bench for a reduced cost. Everybody wins. This ball screw was the X-Axis to a 1998 Hwacheon Hi-ECO 35 or Hieco 35 CNC turning lathe. Noted that the ball nut was a split nut design. The two ball nut halves were cleaned, inspected, and then rebuilt separately. They were then put together on either side of the original spacer shim. If all the math and measurements were correct, the ball screw was rebuilt with the proper preload for the machining process it was dedicated to. A quick way to see if a machine center like this needed ball screw service was to push those spacer shims to see if they moved. If the ball nut had proper drag torque and preload, those shims should not budge at all; they should be compressed together. If they wiggled, it was advisable to give us a call. If field service made the repair budget too costly, a mail-in system for smaller screws like this one could be considered.