Lucas Mill
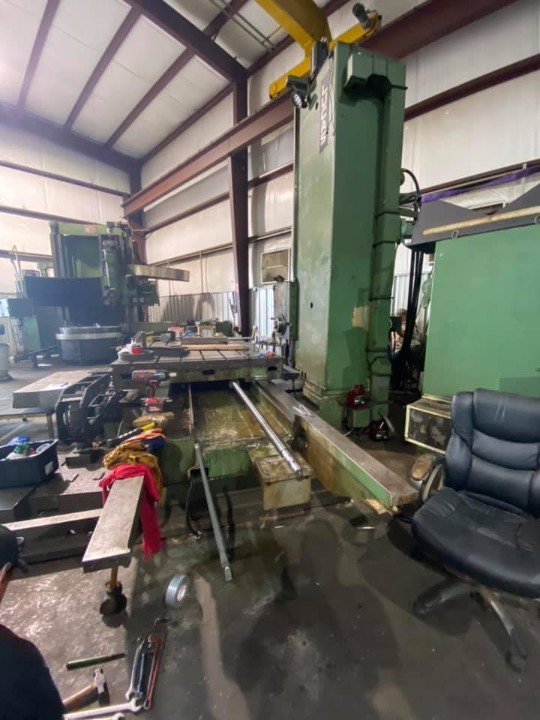
Worked on quite a few of these. There are many models including the 41B, 41B-48, 42B, 441B-48, and 5426-20, and the ball screw for this axis could be from any number of manufacturers, each with their own different way of accessing and rebuilding them. On a machine like this, a ballpark quote was provided, but there may have been some additional charges due to the extra time required to repair. For example, some ball screws could stay within the machine and be rebuilt, while others required the removal of other components in order to access the ball nut for refurbishment. Sometimes, the whole screw assembly had to be removed for rebuild.
The most common scenario involved a well-worn and used Lucas horizontal boring mill purchased at a discounted price, sometimes as scrap. The new owner wanted to bring it back to life, sometimes with a retrofitted controller. Collaboration occurred with many other CNC service companies to make this happen. For inquiries, assistance was offered.
For those with a Lucas mill needing field service ball screw service, it was advised to take photos of the ball screw shaft and the ball nut if possible. This may have required maintenance technicians to pull the covers back and perform some cleaning. However, this procedure helped to provide a more accurate and competitive service quote to tighten up the ball screw assembly.
In this image, notice that the servo motor and end bearing assembly were both completely removed, which was required to service this type of screw system. The thing is, on these older Lucas mills, servicing another similar model type could result in a completely different refurbishment procedure.
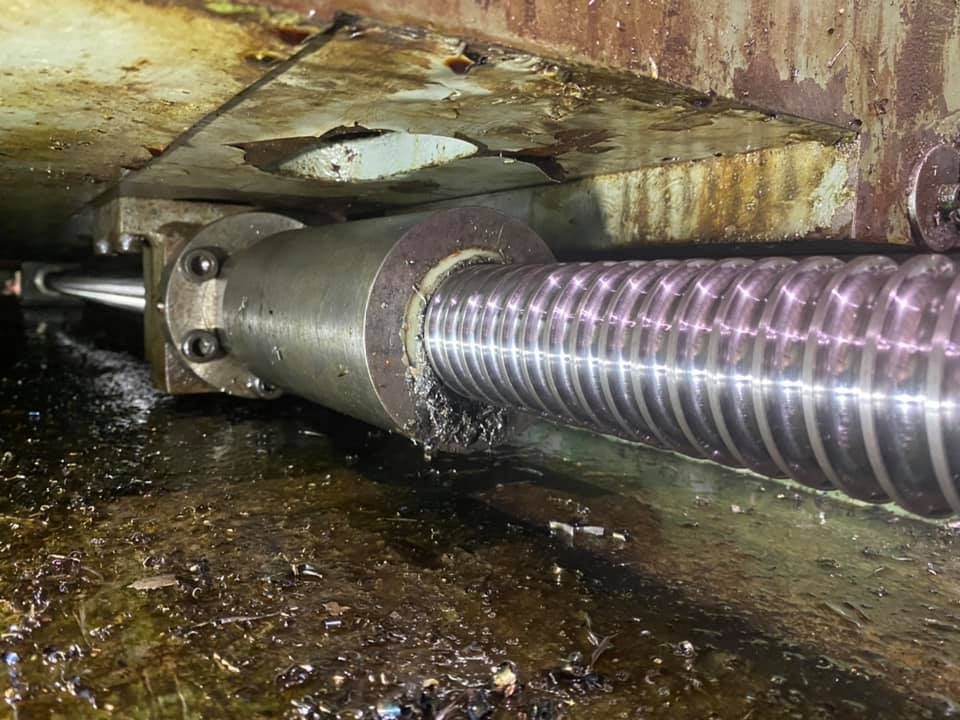
Typical photo from the table X-Axis ball screw on a Lucas Horizontal Boring Mill. The entire operation cavity for the screw had a layer of sticky cutting fluid residue on it. When mixed with sharp debris from years of milling, it made service similar to polishing a porcupine. This ball nut in particular was an internally routed one, meaning the ball bearings inside circulated through milled passages completely inside of the nut. Servicing this type required the motor and end bearing assembly to be completely removed. This particular Lucas was extra joyous to service due to the table ball nut yoke location. It was in the center of the table, meaning multiple socket extensions were pieced together to free the four bolts. Removal of the bolts was not too difficult, but putting them back was a challenge.
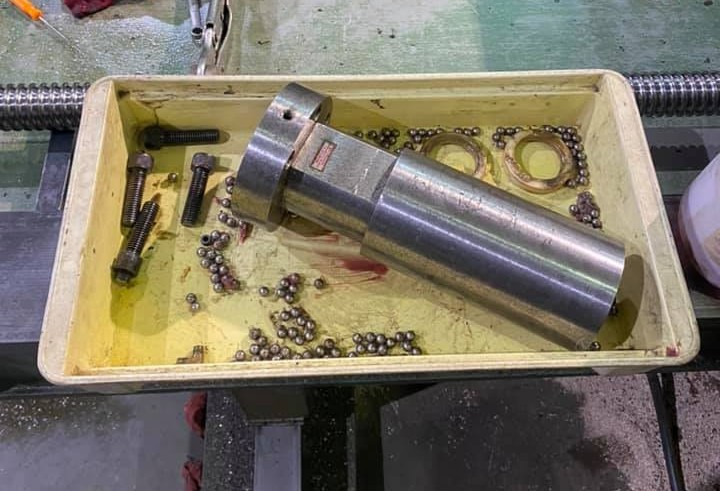
Ball nut was pulled from one of the many Lucas Horizontal Boring Mills serviced over the decades. This one was tricky, as all the balls were internally routed in the ball nut. The ball nut was removed from the ball screw shaft. It was cleaned completely out. If the seals were worn, new ones could be modeled and fabricated. Ball bearings were inspected for size and condition. While this ball nut looked deceptively simple, refurbishing it for an accurate fit sometimes took many hours.
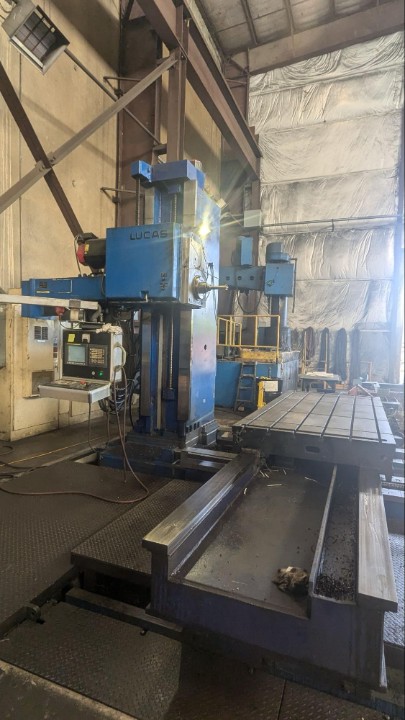
Serviced yet another Lucas horizontal boring mill. Once again, it seemed like the same repair job. The X-Axis table ball screw was loose and needed to be tightened. This one had been retrofitted with a new FANUC controller. Worked with several CNC controller specialists around North America. Always happy to forward a suitable company if assistance was required in updating machine centers.
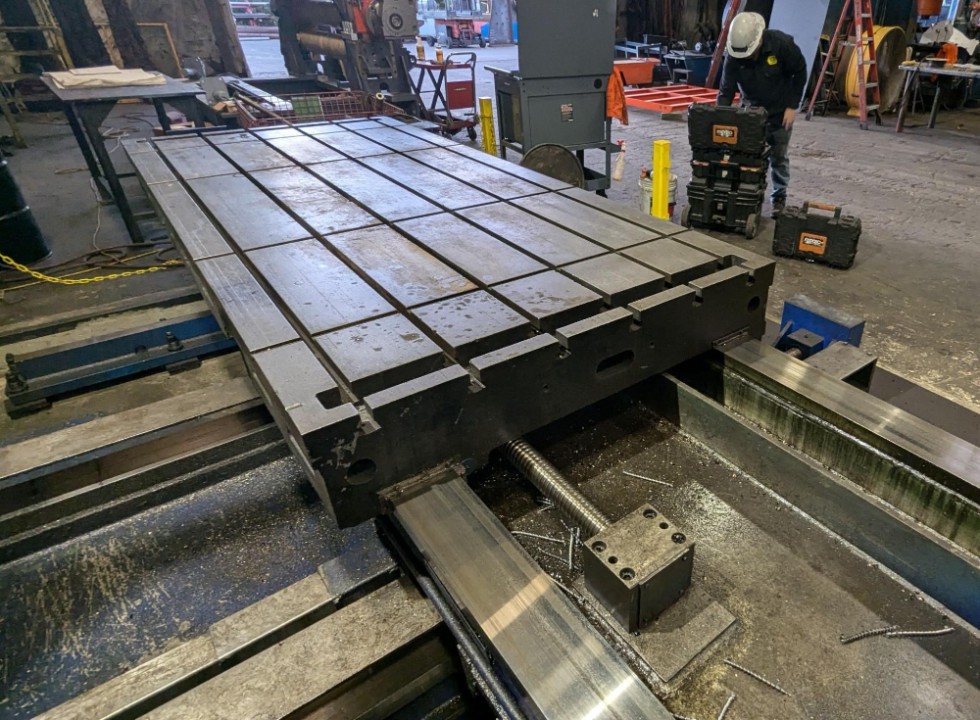
Covers were removed prior to table ball screw service on a Lucas Horizontal Boring Mill. The ball screw shaft was observed on what is referred to as the outboard end bearing side of the ball screw assembly. The servomotor assembly was located on the other side of the machine. On this machine, discoloration of the slideways was noticeable. On this particular model, there was insufficient lubrication for the slideways. This, in turn, forced the servo and the ball screw to operate, moving a much heavier load with more friction. This, in turn, accelerated the wear on the ball nut. Over a period of time, the ball nut wore itself loose.
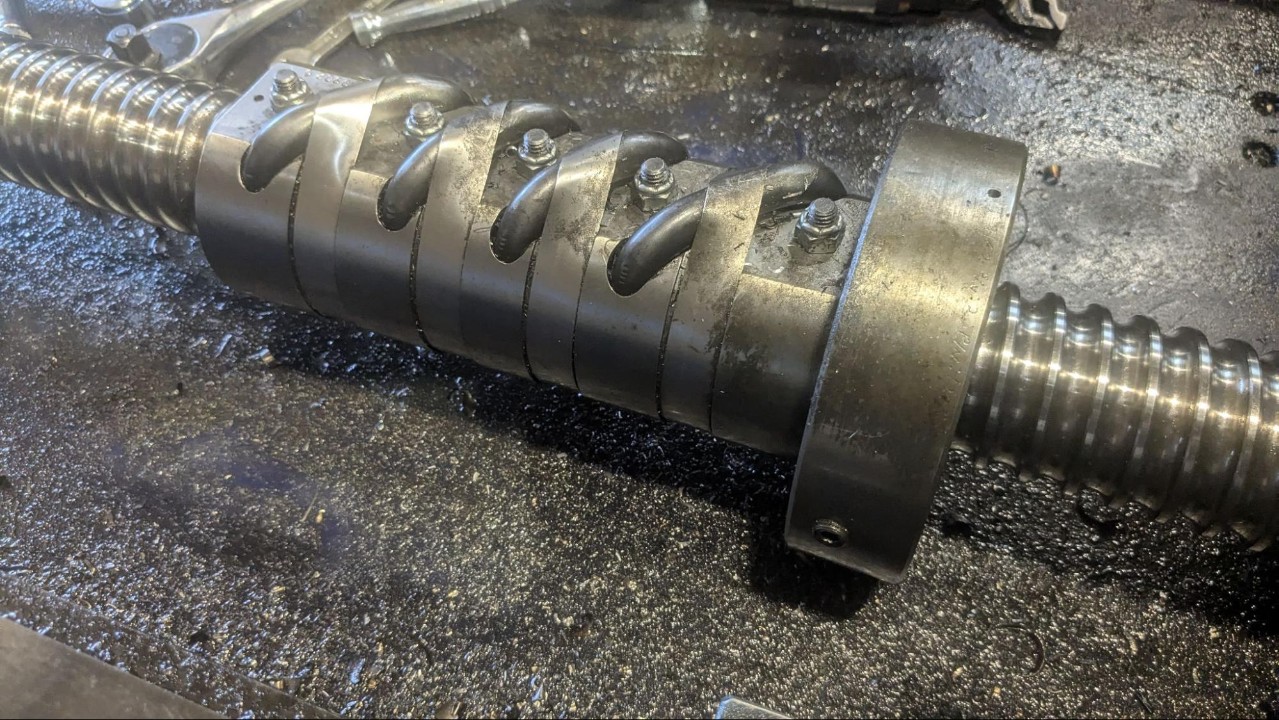
Another random ball nut and ball screw assembly was found in a Lucas Horizontal Boring Mill. Noticed how this ball nut had four externally routed ball bearing return tubes. There were four independent loops of ball bearings on this ball nut. The return tubes were held in place by metal straps. Whenever Ballscrew Guys saw ball nuts like this, it was known that a lower-end ball screw assembly was being dealt with, which would have issues and headaches. The strap method of return tube securing was an inexpensive way to hold the tubes in when there was no desire to add machine time for better methods to hold the tubes in place. Quite frankly, when these were seen, it was known that a ball screw was being examined that most likely was not OEM and had been replaced by the cheapest replacement available. The main issue encountered when servicing crude assemblies like this was that they often skimped on the heat treatment. Ideally, the ball screw assembly had a ball nut and ball screw shaft of equivalent Rockwell hardness, with the ball bearing inside slightly softer. On “strap nuts,” as the technicians liked to call them, the hardness on all components could be all over the place, creating strange wear conditions on the assembly.
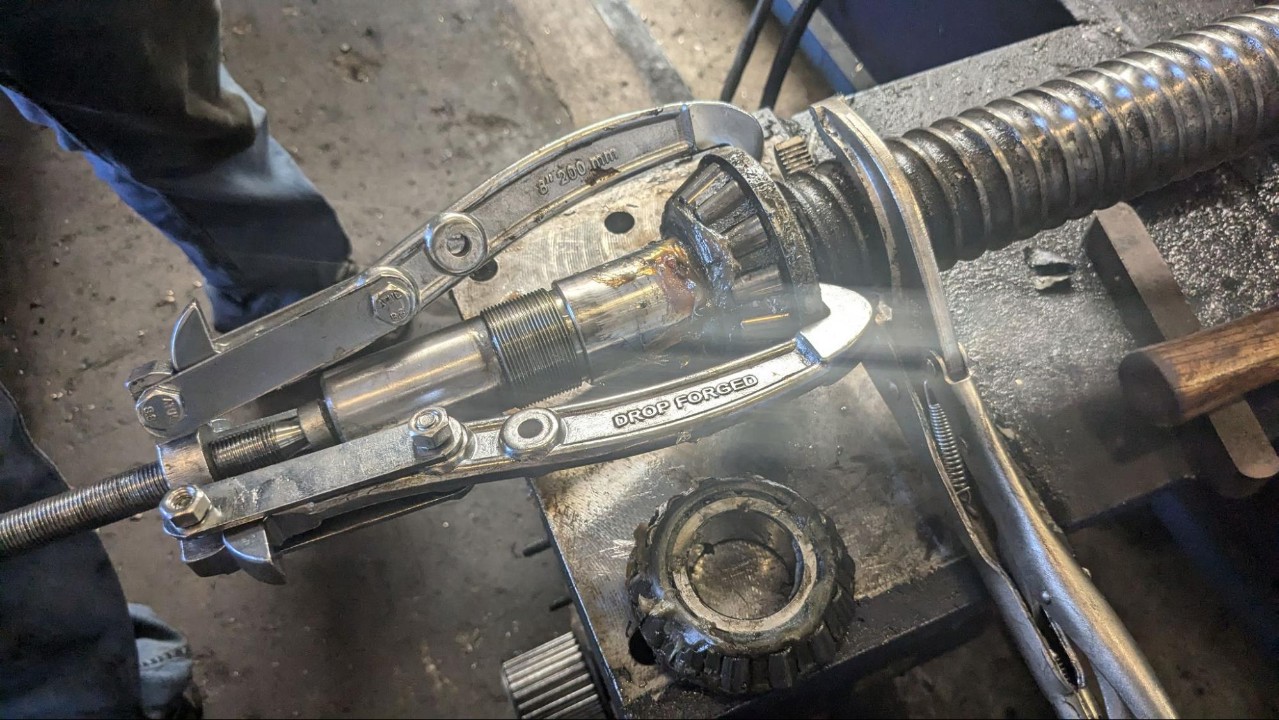
Motor side removal of the tapered roller bearings on the table ball screw of a Lucas Horizontal Boring Mill occurred. Ballscrew Guys often referred to this simply as End Bearing Service. However, there are a variety of bearing types that can be found in the motor and outboard side ball screw mount housings. The most common is angular contact bearings. In this case, this Lucas Mill ran for a period of time with poor preventative maintenance and lubrication scheduling. The lack of lube caused premature wear on the ball nut and end bearing assembly. In time, they wore out, creating looseness. Ballscrew Guys strongly recommended replacing end bearing components whenever they were required for removal to service the ball screw. Looseness in the end bearing assemblies could also be the root cause of lost motion and excessive noise.
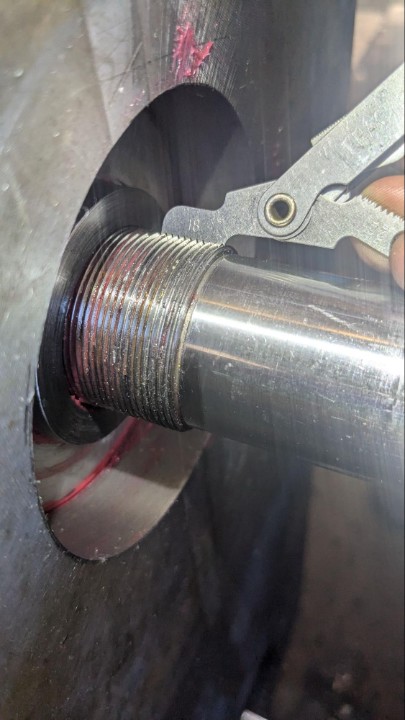
Lucas Horizontal Boring Mill table service. Measured the thread pitch on an X-Axis ball screw. This was the motor side end nut threads, which encapsulated the tapered roller bearings together in the end bearing housing. The threads were measured because they were damaged. A different CNC service contractor was used prior to calling. They performed poor exploratory surgery on this machine. In the process of removing the motor and end bearing housing mount from the machine base, they damaged the threads on the ball screw shaft. Measurements were taken to determine the dimensions. Then the proper die was obtained to rechase the threads, allowing the end nut to thread onto the shaft, providing the proper load and compression to the tapered roller bearings.